ڈاون ہول کیمیکل انجیکشن لائنز - وہ کیوں ناکام ہوتی ہیں؟تجربات، چیلنجز اور ٹیسٹ کے نئے طریقوں کا اطلاق
کاپی رائٹ 2012، سوسائٹی آف پٹرولیم انجینئرز
خلاصہ
Statoil کئی شعبوں کو آپریٹ کر رہا ہے جہاں سکیل انحیبیٹر کا ڈاون ہول لگاتار انجیکشن لگایا جاتا ہے۔مقصد اوپری نلیاں اور حفاظتی والو کو (Ba/Sr) SO4orCaCO سے بچانا ہے۔پیمانہ، ان صورتوں میں جہاں پیمانے کو نچوڑنا مشکل اور مہنگا ہو سکتا ہے مستقل بنیادوں پر انجام دینا، مثلاً ذیلی کھیتوں کا ٹائی ان۔
سکیل انحیبیٹر ڈاون ہول کا لگاتار انجیکشن تکنیکی طور پر مناسب حل ہے کہ کنویں میں اوپری نلیاں اور حفاظتی والو کی حفاظت کریں جن میں پروڈکشن پیکر کے اوپر اسکیلنگ کی صلاحیت موجود ہے۔خاص طور پر ان کنوؤں میں جنہیں کنویں کے قریبی علاقے میں پیمانہ کاری کی صلاحیت کی وجہ سے مستقل بنیادوں پر نچوڑنے کی ضرورت نہیں ہے۔
کیمیائی انجیکشن لائنوں کی ڈیزائننگ، آپریٹنگ اور برقرار رکھنے کے لیے مواد کے انتخاب، کیمیائی قابلیت اور نگرانی پر اضافی توجہ دینے کی ضرورت ہے۔دباؤ، درجہ حرارت، بہاؤ کے نظام اور نظام کی جیومیٹری محفوظ آپریشن کے لیے چیلنجز پیش کر سکتی ہے۔پروڈکشن سہولت سے لے کر سمندری ٹیمپلیٹ تک کئی کلومیٹر لمبی انجیکشن لائنوں اور کنوؤں میں انجیکشن والوز میں چیلنجز کی نشاندہی کی گئی ہے۔
بارش اور سنکنرن کے مسائل سے متعلق ڈاون ہول لگاتار انجیکشن سسٹم کی پیچیدگی کو ظاہر کرنے والے فیلڈ تجربات پر تبادلہ خیال کیا گیا ہے۔لیبارٹری مطالعہ اور کیمیائی قابلیت کے لیے نئے طریقوں کا اطلاقکثیر الشعبہ اقدامات کی ضروریات کو پورا کیا جاتا ہے۔
تعارف
Statoil کئی شعبوں میں کام کر رہا ہے جہاں کیمیکلز کا ڈاون ہول لگاتار انجیکشن لگایا گیا ہے۔اس میں بنیادی طور پر اسکیل انحیبیٹر (SI) کا انجیکشن شامل ہے جہاں مقصد اوپری نلیاں اور ڈاون ہول سیفٹی والو (DHSV) کو (Ba/Sr) SO4orCaCO سے بچانا ہے۔پیمانہبعض صورتوں میں ایملشن بریکر کو ڈاون ہول میں انجکشن لگایا جاتا ہے تاکہ رشتہ دار زیادہ درجہ حرارت پر کنویں کی گہرائی میں علیحدگی کا عمل شروع کیا جا سکے۔
کنویں کے اوپری حصے کی حفاظت کے لیے اسکیل انحیبیٹر ڈاون ہول کا لگاتار انجیکشن تکنیکی طور پر ایک مناسب حل ہے جس میں پروڈکشن پیکر کے اوپر اسکیلنگ کی صلاحیت موجود ہے۔لگاتار انجیکشن لگانے کی سفارش کی جا سکتی ہے خاص طور پر ان کنوؤں میں جنہیں نچوڑنے کی ضرورت نہیں ہے کیونکہ قریب کے کنویں میں اسکیلنگ کی صلاحیت کم ہے۔یا ایسے معاملات میں جہاں پیمانے پر نچوڑنا مشکل اور مہنگا ہو سکتا ہے مستقل بنیادوں پر کارکردگی کا مظاہرہ کرنا، مثال کے طور پر ذیلی کھیتوں کا ٹائی ان۔
Statoil نے مسلسل کیمیائی انجیکشن کے تجربے کو ٹاپ سائیڈ سسٹمز اور سب سی ٹیمپلیٹس تک بڑھایا ہے لیکن نیا چیلنج انجیکشن پوائنٹ کو کنویں میں مزید گہرائی تک لے جانا ہے۔کیمیکل انجیکشن لائنوں کی ڈیزائننگ، آپریٹنگ اور برقرار رکھنے کے لیے کئی موضوعات پر اضافی توجہ دینے کی ضرورت ہے۔جیسے مواد کا انتخاب، کیمیائی قابلیت اور نگرانی۔دباؤ، درجہ حرارت، بہاؤ کے نظام اور نظام کی جیومیٹری محفوظ آپریشن کے لیے چیلنجز پیش کر سکتی ہے۔پیداواری سہولت سے لے کر سمندری ٹیمپلیٹ تک اور کنوؤں کے نیچے انجیکشن والوز تک طویل (کئی کلومیٹر) انجیکشن لائنوں میں چیلنجز کی نشاندہی کی گئی ہے۔تصویر 1۔انجیکشن سسٹم میں سے کچھ نے منصوبہ کے مطابق کام کیا ہے، جبکہ دیگر مختلف وجوہات کی بناء پر ناکام ہو چکے ہیں۔ڈاون ہول کیمیکل انجیکشن (DHCI) کے لیے کئی نئی فیلڈ ترقیات کی منصوبہ بندی کی گئی ہے۔البتہ؛کچھ معاملات میں ابھی تک آلات مکمل طور پر اہل نہیں ہوئے ہیں۔
DHCI کا اطلاق ایک پیچیدہ کام ہے۔اس میں تکمیل اور اچھی طرح سے ڈیزائن، اچھی کیمسٹری، ٹاپ سائیڈ سسٹم اور ٹاپ سائیڈ پروسیس کا کیمیائی خوراک کا نظام شامل ہے۔کیمیکل کو اوپر کی طرف سے کیمیکل انجیکشن لائن کے ذریعے تکمیلی سامان تک اور نیچے کنویں میں پمپ کیا جائے گا۔لہذا، اس قسم کے منصوبے کی منصوبہ بندی اور اس پر عمل درآمد میں کئی شعبوں کے درمیان تعاون بہت ضروری ہے۔مختلف پہلوؤں کا جائزہ لینا ہوگا اور ڈیزائن کے دوران اچھی بات چیت ضروری ہے۔پروسیس انجینئرز، زیر سمندر انجینئرز اور تکمیل انجینئرز شامل ہیں، اچھی کیمسٹری، مواد کے انتخاب، بہاؤ کی یقین دہانی اور پیداوار کیمیکل مینجمنٹ کے موضوعات سے نمٹنے کے لئے.چیلنجز کیمیکل گن کنگ یا درجہ حرارت میں استحکام، سنکنرن اور بعض صورتوں میں کیمیکل انجیکشن لائن میں مقامی دباؤ اور بہاؤ کے اثرات کی وجہ سے ویکیوم اثر ہو سکتا ہے۔ان کے علاوہ، ہائی پریشر، ہائی ٹمپریچر، ہائی گیس ریٹ، ہائی اسکیلنگ پوٹینشل جیسے حالات,کنویں میں لمبی دوری کی نال اور گہرا انجیکشن پوائنٹ، انجیکشن والے کیمیکل اور انجیکشن والو کو مختلف تکنیکی چیلنجز اور ضروریات فراہم کرتا ہے۔
Statoil آپریشنز میں نصب DHCI سسٹمز کا ایک جائزہ ظاہر کرتا ہے کہ تجربہ ہمیشہ کامیاب نہیں رہا جدول 1۔ تاہم، انجیکشن ڈیزائن، کیمیائی قابلیت، آپریشن اور دیکھ بھال کی بہتری کے لیے منصوبہ بندی کی جا رہی ہے۔چیلنجز فیلڈ سے فیلڈ میں مختلف ہوتے ہیں، اور مسئلہ ضروری نہیں ہے کہ کیمیائی انجیکشن والو خود کام نہیں کر رہا ہے۔
پچھلے برسوں میں ڈاون ہول کیمیکل انجیکشن لائنوں سے متعلق کئی چیلنجز کا سامنا ہوا ہے۔اس مقالے میں ان تجربات سے چند مثالیں پیش کی گئی ہیں۔اس مقالے میں چیلنجز اور DHCI لائنوں سے متعلق مسائل کو حل کرنے کے لیے اٹھائے گئے اقدامات پر تبادلہ خیال کیا گیا ہے۔دو کیس ہسٹری دی گئی ہیں؛ایک سنکنرن پر اور ایک کیمیکل گن کنگ پر۔بارش اور سنکنرن کے مسائل سے متعلق ڈاون ہول لگاتار انجیکشن سسٹم کی پیچیدگی کو ظاہر کرنے والے فیلڈ تجربات پر تبادلہ خیال کیا گیا ہے۔
لیبارٹری مطالعہ اور کیمیائی قابلیت کے لیے نئے طریقوں کے اطلاق پر بھی غور کیا جاتا ہے۔کیمیکل کو کیسے پمپ کیا جائے، اسکیلنگ کی صلاحیت اور روک تھام، پیچیدہ آلات کا استعمال اور جب کیمیکل دوبارہ تیار کیا جائے گا تو کیمیکل اوپر والے نظام کو کیسے متاثر کرے گا۔کیمیائی استعمال کے معیار کو قبول کرنے میں ماحولیاتی مسائل، کارکردگی، ذخیرہ کرنے کی صلاحیت اوپر کی طرف، پمپ کی شرح، کیا موجودہ پمپ استعمال کیا جا سکتا ہے وغیرہ شامل ہیں۔ تکنیکی سفارشات سیال اور کیمسٹری کی مطابقت، بقایا کا پتہ لگانے، مواد کی مطابقت، زیر سمندر نال ڈیزائن، کیمیائی خوراک کے نظام پر مبنی ہونی چاہئیں۔ اور ان لائنوں کے ماحول میں مواد۔انجیکشن لائن کو گیس کے حملے سے روکنے کے لیے کیمیکل کو ہائیڈریٹ کرنے کی ضرورت ہو سکتی ہے اور کیمیکل کو ٹرانسپورٹ اور اسٹوریج کے دوران جمنا نہیں چاہیے۔موجودہ داخلی رہنما خطوط میں ایک چیک لسٹ موجود ہے جس میں سسٹم میں ہر ایک نقطہ پر کیمیکل لگائے جاسکتے ہیں جسمانی خصوصیات جیسے viscosity اہم ہیں۔انجیکشن سسٹم نال کے زیریں بہاؤ لائن کا 3-50 کلومیٹر کا فاصلہ اور کنویں میں 1-3 کلومیٹر نیچے کا اشارہ کر سکتا ہے۔لہذا، درجہ حرارت کی استحکام بھی اہم ہے.بہاو اثرات کی تشخیص، مثال کے طور پر ریفائنریوں میں بھی غور کیا جا سکتا ہے.
ڈاون ہول کیمیکل انجیکشن سسٹم
لاگت کا فائدہ
ڈی ایچ ایس کی حفاظت کے لیے اسکیل انحیبیٹر ڈاون ہول کا لگاتار انجیکشن لگانا شاید اسکیل انحیبیٹر کے ساتھ کنویں کو نچوڑنے کے مقابلے میں پروڈکشن نلیاں لاگت سے موثر ہو۔یہ ایپلیکیشن اسکیل سکوز ٹریٹمنٹ کے مقابلے میں تشکیل کو پہنچنے والے نقصان کے امکانات کو کم کرتی ہے، اسکیل نچوڑنے کے بعد پروسیسنگ کے مسائل کے امکانات کو کم کرتی ہے اور ٹاپ سائیڈ انجیکشن سسٹم سے کیمیائی انجیکشن کی شرح کو کنٹرول کرنے کا امکان فراہم کرتی ہے۔انجیکشن سسٹم کو دوسرے کیمیکلز کو مسلسل نیچے کی طرف انجیکشن لگانے کے لیے بھی استعمال کیا جا سکتا ہے اور اس طرح دیگر چیلنجوں کو کم کیا جا سکتا ہے جو پروسیس پلانٹ کو مزید نیچے کی طرف لے جا سکتے ہیں۔
Oseberg S یا فیلڈ کی ڈاون ہول اسکیل حکمت عملی تیار کرتے ہوئے ایک جامع مطالعہ کیا گیا ہے۔بڑے پیمانے پر تشویش CaCO تھی؛اوپری نلیاں میں اسکیلنگ اور ممکنہ DHSV کی ناکامی۔Oseberg S یا پیمانے کے انتظام کی حکمت عملی کے تحفظات نے یہ نتیجہ اخذ کیا کہ تین سال کی مدت میں، DHCI ان کنوؤں میں جہاں کیمیکل انجیکشن لائنیں کام کر رہی تھیں، سب سے زیادہ لاگت والا حل تھا۔اسکیل سکوز کی مسابقتی تکنیک کے حوالے سے بنیادی لاگت کا عنصر کیمیائی/آپریشنل لاگت کے بجائے موخر تیل تھا۔گیس لفٹ میں اسکیل انہیبیٹر کے اطلاق کے لیے، کیمیکل لاگت کا سب سے بڑا عنصر گیس لفٹ کی اونچی شرح تھی جس کی وجہ سے ہائی ایس آئی ارتکاز ہوتا ہے، کیونکہ کیمیکل گن کنگ سے بچنے کے لیے ارتکاز کو گیس لفٹ کی شرح کے ساتھ متوازن رکھنا پڑتا ہے۔Oseberg S کے دو کنوؤں کے لیے یا جن میں DHC I لائنیں اچھی طرح سے کام کر رہی ہیں، اس اختیار کا انتخاب DHS V کی CaCO کے خلاف حفاظت کے لیے کیا گیا تھا۔پیمانہ کاری
مسلسل انجیکشن سسٹم اور والوز
مسلسل کیمیکل انجیکشن سسٹم کا استعمال کرتے ہوئے موجودہ تکمیلی حل کو کیپلری لائنوں کے پلگ ان کو روکنے کے لیے چیلنجوں کا سامنا ہے۔عام طور پر انجیکشن سسٹم ایک کیپلیری لائن پر مشتمل ہوتا ہے، 1/4" یا 3/8" بیرونی قطر (OD)، جو سطح کے کئی گنا تک جڑی ہوتی ہے، اس کے ذریعے کھلائی جاتی ہے اور نلکی کے کنڈلی طرف والے نلکے کے ہینگر سے جڑی ہوتی ہے۔کیپلیری لائن پروڈکشن ٹیوبنگ کے بیرونی قطر کے ساتھ خصوصی نلیاں کالر کلیمپ کے ذریعے منسلک ہوتی ہے اور نلیاں کے باہر کیمیکل انجیکشن مینڈریل تک پوری طرح چلتی ہے۔مینڈریل کو روایتی طور پر ڈی ایچ ایس V کے اوپر یا کنویں میں اس سے زیادہ گہرائی میں رکھا جاتا ہے تاکہ انجکشن والے کیمیکل کو پھیلانے کا کافی وقت دیا جائے اور اس کیمیکل کو وہیں رکھا جائے جہاں چیلنجز پائے جائیں۔
کیمیکل انجیکشن والو، Fig.2 پر، تقریباً 1.5 انچ قطر کا ایک چھوٹا کارتوس چیک والوز پر مشتمل ہوتا ہے جو کیپلیری لائن میں داخل ہونے سے کنویں کے سیال کو روکتا ہے۔یہ صرف ایک چھوٹا سا پاپیٹ ہے جو ایک چشمے پر سوار ہے۔سپرنگ فورس سیلنگ سیٹ سے پاپیٹ کو کھولنے کے لیے درکار دباؤ کو سیٹ اور پیشن گوئی کرتی ہے۔جب کیمیکل بہنا شروع ہو جاتا ہے، تو پاپیٹ اپنی سیٹ سے اٹھا کر چیک والو کھول دیتا ہے۔
اسے دو چیک والوز لگانے کی ضرورت ہے۔ایک والو وہ بنیادی رکاوٹ ہے جو ویلبور سیالوں کو کیپلیری لائن میں داخل ہونے سے روکتی ہے۔اس میں نسبتاً کم اوپننگ پریشر ہوتا ہے (2-15bars) .اگر کیپلیری لائن کے اندر ہائیڈرو سٹیٹک پریشر ویلبور پریشر سے کم ہے، تو ویلبور سیال کیپلیری لائن میں داخل ہونے کی کوشش کریں گے۔دوسرے چیک والو میں 130-250 سلاخوں کا غیر معمولی اوپننگ پریشر ہوتا ہے اور اسے U-tube روک تھام کے نظام کے نام سے جانا جاتا ہے۔یہ والو کیپلیری لائن کے اندر کیمیکل کو آزادانہ طور پر ویلبور میں بہنے سے روکتا ہے اگر کیپلیری لائن کے اندر ہائیڈرو سٹیٹک پریشر پروڈکشن نلیاں کے اندر کیمیائی انجیکشن پوائنٹ پر ویل بور کے دباؤ سے زیادہ ہو۔
دو چیک والوز کے علاوہ، عام طور پر ایک ان لائن فلٹر ہوتا ہے، اس کا مقصد اس بات کو یقینی بنانا ہے کہ کسی بھی قسم کا کوئی ملبہ چیک والو کے نظام کی سیل کرنے کی صلاحیتوں کو خطرے میں نہ ڈال سکے۔
بیان کردہ چیک والوز کے سائز کافی چھوٹے ہیں، اور انجکشن والے سیال کی صفائی ان کی آپریشنل فعالیت کے لیے ضروری ہے۔یہ خیال کیا جاتا ہے کہ نظام میں موجود ملبے کو کیپلیری لائن کے اندر بہاؤ کی شرح کو بڑھا کر دور کیا جا سکتا ہے، تاکہ چیک والوز جان بوجھ کر کھل جائیں۔
جب چیک والو کھلتا ہے، بہتا ہوا دباؤ تیزی سے کم ہوتا ہے اور کیپلیری لائن تک پھیلتا ہے جب تک کہ دباؤ دوبارہ نہ بڑھ جائے۔چیک والو تب تک بند ہو جائے گا جب تک کہ کیمیکل کا بہاؤ والو کو کھولنے کے لیے کافی دباؤ نہیں بناتا۔نتیجہ چیک والو کے نظام میں دباؤ دولن ہے۔چیک والو سسٹم میں اوپننگ پریشر جتنا زیادہ ہوتا ہے، جب چیک والو کھلتا ہے اور سسٹم متوازن حالات کو حاصل کرنے کی کوشش کرتا ہے تو کم بہاؤ کا علاقہ قائم ہوتا ہے۔
کیمیائی انجیکشن والوز کا افتتاحی دباؤ نسبتاً کم ہوتا ہے۔اور اگر کیمیکل انلیٹ پوائنٹ پر نلیاں کا دباؤ کیپلیری لائن کے اندر کیمیکلز کے ہائیڈرو سٹیٹک دباؤ کے علاوہ چیک والو کھولنے کے دباؤ سے کم ہو جائے تو کیپلیری لائن کے اوپری حصے میں ویکیوم یا ویکیوم کے قریب واقع ہوگا۔جب کیمیکل کا انجیکشن رک جاتا ہے یا کیمیکل کا بہاؤ کم ہوتا ہے تو کیپلیری لائن کے اوپری حصے میں ویکیوم کے قریب حالات پیدا ہونا شروع ہو جائیں گے۔
ویکیوم کی سطح کا انحصار ویلبور پریشر، کیپلیری لائن کے اندر استعمال ہونے والے انجکشن شدہ کیمیکل مکسچر کی مخصوص کشش ثقل، انجیکشن پوائنٹ پر چیک والو کھولنے کا دباؤ اور کیپلیری لائن کے اندر کیمیکل کے بہاؤ کی شرح پر ہوتا ہے۔اچھی حالتیں فیلڈ کی زندگی بھر میں مختلف ہوں گی اور ویکیوم کا امکان بھی اوور ٹائم میں مختلف ہوگا۔متوقع چیلنجوں کے پیش آنے سے پہلے صحیح غور اور احتیاط کرنے کے لیے اس صورتحال سے آگاہ ہونا ضروری ہے۔
کم انجیکشن کی شرحوں کے ساتھ، عام طور پر اس قسم کی ایپلی کیشنز میں استعمال ہونے والے سالوینٹس بخارات بن کر ایسے اثرات پیدا کر رہے ہیں جن کی پوری طرح سے تحقیق نہیں کی گئی ہے۔یہ اثرات گن کنگ ہیں یا ٹھوس اشیاء کی بارش، مثال کے طور پر پولیمر، جب سالوینٹ بخارات بن رہا ہوتا ہے۔
مزید، کیمیکل کی سیال سطح اور اوپر کے قریب ویکیوم گیس کے مرحلے سے بھرے بخارات کے درمیان منتقلی کے مرحلے میں گالوانک خلیات بن سکتے ہیں۔یہ ان حالات میں کیمیکل کی بڑھتی ہوئی جارحیت کے نتیجے میں کیپلیری لائن کے اندر مقامی پٹنگ سنکنرن کا باعث بن سکتا ہے۔فلیکس یا نمک کے کرسٹل کیپلیری لائن کے اندر ایک فلم کے طور پر بنتے ہیں کیونکہ اس کا اندرونی حصہ سوکھ جاتا ہے اور کیپلیری لائن کو جام یا پلگ کر سکتا ہے۔
ویسے رکاوٹ فلسفہ
مضبوط کنویں کے حل کو ڈیزائن کرتے وقت، Statoil کا تقاضا ہے کہ کنویں کے لائف سائیکل کے دوران کنویں کی حفاظت ہر وقت موجود ہو۔اس طرح، Statoil کا تقاضا ہے کہ دو آزاد کنویں کی رکاوٹیں برقرار ہیں۔تصویر 3 غیر معمولی کنویں کی رکاوٹ کو ظاہر کرتا ہے، جہاں نیلا رنگ بنیادی کنویں رکاوٹ کے لفافے کی نمائندگی کرتا ہے۔اس صورت میں پیداوار نلیاں.سرخ رنگ ثانوی رکاوٹ کے لفافے کی نمائندگی کرتا ہے۔سانچےخاکے میں بائیں طرف کیمیکل انجیکشن کو بلیک لائن کے طور پر اشارہ کیا گیا ہے جس میں انجیکشن پوائنٹ کے ساتھ سرخ نشان والے علاقے میں پیداواری نلیاں (ثانوی رکاوٹ) ہیں۔کنویں میں کیمیائی انجیکشن سسٹم متعارف کروانے سے، دونوں بنیادی اور ثانوی کنویں کی رکاوٹیں خطرے میں پڑ جاتی ہیں۔
سنکنرن پر کیس کی تاریخ
واقعات کی ترتیب
نارویجن کانٹی نینٹل شیلف پر Statoil کے ذریعے چلائے جانے والے آئل فیلڈ میں اسکیل انحیبیٹر کا ڈاون ہول کیمیکل انجیکشن لگایا گیا ہے۔اس معاملے میں لاگو پیمانے پر روکنے والا اصل میں ٹاپ سائیڈ اور سب سی ایپ کے لیے اہل تھا۔کنویں کی دوبارہ تکمیل کے بعد DHCIpointat2446mMD کی تنصیب کی گئی، تصویر 3۔کیمیکل کی مزید جانچ کیے بغیر ٹاپ سائیڈ اسکیل انحیبیٹر کا ڈاون ہول انجیکشن شروع کیا گیا تھا۔
ایک سال کے آپریشن کے بعد کیمیکل انجیکشن سسٹم میں لیکیجز دیکھے گئے اور تحقیقات شروع کی گئیں۔رساو نے کنویں کی رکاوٹوں پر نقصان دہ اثر ڈالا۔اسی طرح کے واقعات کئی کنوؤں کے لیے پیش آئے اور ان میں سے کچھ کو تحقیقات کے دوران بند کرنا پڑا۔
پروڈکشن نلیاں کھینچی گئیں اور تفصیل سے مطالعہ کیا گیا۔سنکنرن کا حملہ نلیاں کے ایک طرف تک محدود تھا، اور کچھ نلیاں کے جوڑ اس قدر زنگ آلود تھے کہ ان کے ذریعے درحقیقت سوراخ ہو گئے تھے۔تقریباً 8.5 ملی میٹر موٹا 3% کروم سٹیل 8 ماہ سے بھی کم عرصے میں بکھر گیا تھا۔کنویں کے اوپری حصے میں مرکزی سنکنرن واقع ہوئی تھی، کنویں کے نیچے سے لے کر تقریباً 380m MD تک، اور تقریباً 350m MD پر سب سے زیادہ خراب نلیاں کے جوڑ پائے گئے۔اس گہرائی کے نیچے بہت کم یا کوئی سنکنرن نہیں دیکھا گیا، لیکن OD's نلیاں پر بہت زیادہ ملبہ پایا گیا۔
9-5/8'' کیسنگ کو بھی کاٹ کر کھینچا گیا اور اسی طرح کے اثرات دیکھے گئے۔صرف ایک طرف کنویں کے اوپری حصے میں سنکنرن کے ساتھ۔حوصلہ افزائی لیک کیسنگ کے کمزور حصے کو پھٹنے کی وجہ سے ہوئی تھی۔
کیمیکل انجیکشن لائن میٹریل الائے 825 تھا۔
کیمیائی قابلیت
کیمیائی خصوصیات اور سنکنرن کی جانچ اسکیل انحیبیٹرز کی اہلیت میں اہم فوکس ہیں اور اصل پیمانہ روکنے والا کوالیفائی کیا گیا تھا اور کئی سالوں سے ٹاپ سائیڈ اور سبسیا ایپلی کیشنز میں استعمال کیا گیا تھا۔اصل کیمیکل ڈاون ہول کو لاگو کرنے کی وجہ موجودہ ڈاون ہول کیمیکل کو تبدیل کرکے ماحولیاتی خصوصیات کو بہتر بنانا تھا تاہم، پیمانہ روکنے والا صرف محیطی اوپر کی طرف اور سمندری فرش کے درجہ حرارت (4-20 ℃) پر استعمال ہوتا تھا۔جب کنویں میں انجکشن لگایا جاتا ہے تو کیمیکل کا درجہ حرارت 90 ℃ تک ہوسکتا ہے، لیکن اس درجہ حرارت پر مزید کوئی جانچ نہیں کی گئی تھی۔
ابتدائی corrosivity ٹیسٹ کیمیکل سپلائر کی طرف سے کئے گئے تھے اور نتائج نے اعلی درجہ حرارت پر کاربن سٹیل کے لئے 2-4mm/سال دکھایا۔اس مرحلے کے دوران آپریٹر کی مادی تکنیکی قابلیت کی کم سے کم شمولیت تھی۔بعد میں آپریٹر کے ذریعہ نئے ٹیسٹ کیے گئے جس سے یہ ظاہر ہوتا ہے کہ پیمانہ روکنے والا پروڈکشن نلیاں اور پروڈکشن کیسنگ میں موجود مواد کے لیے انتہائی سنکنرن ہے، سنکنرن کی شرح 70mm/سال سے زیادہ ہے۔انجیکشن سے پہلے کیمیکل انجیکشن لائن میٹریل الائے 825 کا اسکیل انحیبیٹر کے خلاف تجربہ نہیں کیا گیا تھا۔کنویں کا درجہ حرارت 90 ℃ تک پہنچ سکتا ہے اور ان حالات میں مناسب ٹیسٹ کرائے جانے چاہئیں۔
تحقیقات سے یہ بھی انکشاف ہوا ہے کہ پیمانہ روکنے والے نے بطور مرتکز حل <3.0 کا پی ایچ رپورٹ کیا تھا۔تاہم، پی ایچ کی پیمائش نہیں کی گئی تھی.بعد میں ماپی گئی پی ایچ نے پی ایچ 0-1 کی بہت کم قدر ظاہر کی۔یہ دی گئی پی ایچ اقدار کے علاوہ پیمائش اور مادی غور و فکر کی ضرورت کو واضح کرتا ہے۔
نتائج کی تشریح
انجیکشن لائن (تصویر 3) اسکیل انحیبیٹر کا ہائیڈرو سٹیٹک پریشر دینے کے لیے بنائی گئی ہے جو انجیکشن پوائنٹ پر کنویں میں دباؤ سے زیادہ ہے۔روکنے والے کو ویلبور میں موجود سے زیادہ دباؤ پر انجیکشن لگایا جاتا ہے۔اس کے نتیجے میں کنویں کے بند ہونے پر یو ٹیوب اثر ہوتا ہے۔والو ہمیشہ کنویں کی نسبت انجیکشن لائن میں زیادہ دباؤ کے ساتھ کھلے گا۔لہذا انجیکشن لائن میں ویکیوم یا بخارات پیدا ہوسکتے ہیں۔سالوینٹس کے بخارات بننے کی وجہ سے گیس/ مائع ٹرانزیشن زون میں سنکنرن کی شرح اور گڑھے کا خطرہ سب سے زیادہ ہے۔کوپن پر کئے گئے لیبارٹری تجربات نے اس نظریہ کی تصدیق کی۔کنویں میں جہاں رساو کا تجربہ ہوا تھا، انجیکشن لائنوں کے تمام سوراخ کیمیکل انجیکشن لائن کے اوپری حصے میں واقع تھے۔
تصویر 4 DHC I لائن کی فوٹو گرافی کو ظاہر کرتا ہے جس میں اہم پٹنگ سنکنرن ہے۔بیرونی پروڈکشن نلیاں پر دیکھے جانے والے سنکنرن نے پٹنگ لیکیج پوائنٹ سے پیمانے پر روکنے والے کی مقامی نمائش کی نشاندہی کی۔یہ رساو انتہائی corrosive کیمیکل کی وجہ سے سنکنرن اور پروڈکشن کیسنگ میں کیمیکل انجیکشن لائن کے ذریعے رساو کی وجہ سے ہوا تھا۔اسکیل انحیبیٹر کو پٹی ہوئی کیپلیری لائن سے کیسنگ اور نلیاں تک اسپرے کیا گیا اور لیک ہونے لگے۔انجیکشن لائن میں لیک کے کسی بھی ثانوی نتائج پر غور نہیں کیا گیا تھا۔یہ نتیجہ اخذ کیا گیا کہ کیسنگ اور نلیاں کا سنکنرن کنسنٹریٹڈ اسکیل انحیبیٹرز کا نتیجہ تھا جو گڑھے والی کیپلیری لائن سے کیسنگ اور نلیاں تک دعا کرتے تھے، تصویر 5۔
اس معاملے میں مادی قابلیت کے انجینئرز کی شمولیت کی کمی تھی۔DHCI لائن پر کیمیکل کی خرابی کی جانچ نہیں کی گئی تھی اور رساو کی وجہ سے ثانوی اثرات کا جائزہ نہیں لیا گیا تھا۔جیسے کہ آیا ارد گرد کا مواد کیمیائی نمائش کو برداشت کر سکتا ہے۔
کیمیکل گن کنگ کی کیس ہسٹری
واقعات کی ترتیب
HP HT فیلڈ کے لیے پیمانے کی روک تھام کی حکمت عملی ڈاون ہول سیفٹی والو کو اوپر کی طرف اسکیل انحیبیٹر کا لگاتار انجیکشن تھا۔کنویں میں ایک شدید کیلشیم کاربونیٹ اسکیلنگ صلاحیت کی نشاندہی کی گئی۔چیلنجوں میں سے ایک اعلی درجہ حرارت اور اعلی گیس اور کنڈینسیٹ کی پیداوار کی شرح کم پانی کی پیداوار کی شرح کے ساتھ مل کر تھی۔اسکیل انحیبیٹر کو انجیکشن لگانے سے تشویش یہ تھی کہ سالوینٹس کو گیس کی اعلی پیداوار کی شرح سے چھین لیا جائے گا اور کیمیکل کا گن کنگ کنویں میں حفاظتی والو کے اوپری حصے میں انجیکشن پوائنٹ پر واقع ہوگا، تصویر 1۔
پیمانہ روکنے والے کی اہلیت کے دوران توجہ HP HT حالات میں پروڈکٹ کی کارکردگی پر تھی جس میں ٹاپ سائیڈ پروسیس سسٹم (کم درجہ حرارت) میں برتاؤ شامل تھا۔گیس کی اونچی شرح کی وجہ سے پیداواری نلیاں میں خود پیمانہ روکنے والے کی بارش سب سے بڑی تشویش تھی۔لیبارٹری ٹیسٹ سے پتہ چلتا ہے کہ پیمانہ روکنے والا نلکی کی دیوار کو تیز کر سکتا ہے اور اس پر عمل کر سکتا ہے۔اس وجہ سے حفاظتی والو کا آپریشن خطرے کو شکست دے سکتا ہے۔
تجربے سے معلوم ہوا کہ چند ہفتوں کے آپریشن کے بعد کیمیکل لائن لیک ہو رہی تھی۔کیپلیری لائن میں نصب سطح کے گیج پر ویل بور کے دباؤ کی نگرانی کرنا ممکن تھا۔اچھی طرح سے سالمیت حاصل کرنے کے لیے لائن کو الگ تھلگ کر دیا گیا تھا۔
کیمیکل انجیکشن لائن کو کنویں سے نکالا گیا، اسے کھولا گیا اور اس کا معائنہ کیا گیا تاکہ مسئلہ کی تشخیص اور ناکامی کی ممکنہ وجوہات کا پتہ لگایا جا سکے۔جیسا کہ تصویر 6 میں دیکھا جا سکتا ہے، پریزیٹیٹ کی نمایاں مقدار پائی گئی اور کیمیائی تجزیے سے معلوم ہوا کہ اس میں سے کچھ پیمانہ روکنے والا تھا۔پریسیپیٹیٹ سیل اور پاپیٹ پر واقع تھا اور والو کو چلایا نہیں جا سکتا تھا۔
والو کی خرابی والو سسٹم کے اندر موجود ملبے کی وجہ سے ہوئی تھی جس کی وجہ سے چیک والوز کو دھات سے دھات کی سیٹ پر کھانے سے روکا جاتا تھا۔ملبے کی جانچ کی گئی اور اہم ذرات دھاتی شیونگ ثابت ہوئے، جو شاید کیپلیری لائن کی تنصیب کے عمل کے دوران پیدا ہوئے تھے۔اس کے علاوہ، دونوں چیک والوز پر خاص طور پر والوز کے پچھلے حصے پر کچھ سفید ملبے کی نشاندہی کی گئی۔یہ کم دباؤ والی سائیڈ ہے، یعنی یہ سائیڈ ہمیشہ ویلبور فلوئڈز کے ساتھ رابطے میں رہے گی۔ابتدائی طور پر، یہ پروڈکشن ویلبور کا ملبہ سمجھا جاتا تھا کیونکہ والوز کھلے ہوئے تھے اور کنویں کے سیالوں کے سامنے آ گئے تھے۔لیکن جانچ پڑتال سے یہ ثابت ہوا کہ ملبے سے ملتے جلتے کیمسٹری والے پولیمر تھے جیسا کہ اسکیل روکنے والے کے طور پر استعمال کیا جاتا ہے۔اس سے ہماری دلچسپی بڑھ گئی اور Statoil کیپلیری لائن میں موجود ان پولیمر ملبے کے پیچھے وجوہات کو تلاش کرنا چاہتا تھا۔
کیمیائی قابلیت
HP HT فیلڈ میں پیداوار کے مختلف مسائل کو کم کرنے کے لیے موزوں کیمیکلز کے انتخاب کے سلسلے میں بہت سے چیلنجز ہیں۔مسلسل انجیکشن ڈاون ہول کے لیے پیمانہ روکنے والے کی اہلیت میں، درج ذیل ٹیسٹ کیے گئے:
● پروڈکٹ کا استحکام
● تھرمل عمر بڑھنا
● متحرک کارکردگی کے ٹیسٹ
● فارمیشن واٹر اور ہائیڈریٹ انحیبیٹر (MEG) کے ساتھ مطابقت
● جامد اور متحرک گن کنگ ٹیسٹ
● دوبارہ تحلیل معلومات پانی، تازہ کیمیکل اور MEG
کیمیکل پہلے سے طے شدہ خوراک کی شرح پر لگایا جائے گا۔,لیکن ضروری نہیں کہ پانی کی پیداوار مستقل ہو۔,یعنی پانی slugging.پانی کی سلگس کے درمیان,جب کیمیکل کنویں میں داخل ہوتا ہے۔,یہ ایک گرم کی طرف سے ملاقات کی جائے گی,ہائیڈرو کاربن گیس کا تیز بہاؤ۔یہ گیس لفٹ ایپلی کیشن (Fleming etal.2003) میں اسکیل انہیبیٹر لگانے کے مترادف ہے۔
اعلی گیس درجہ حرارت,سالوینٹ اتارنے کا خطرہ بہت زیادہ ہے اور گن کنگ انجیکشن والو کی رکاوٹ کا سبب بن سکتا ہے۔یہ ہائی بوائلنگ پوائنٹ/کم بخارات کے دباؤ والے سالوینٹس اور دیگر وانپ پریشر ڈپریسنٹ (VPD's) کے ساتھ تیار کردہ کیمیکلز کے لیے بھی خطرہ ہے۔ جزوی رکاوٹ کی صورت میں,تشکیل پانی کا بہاؤ,MEG اور/یا تازہ کیمیکل پانی کی کمی یا گنک آؤٹ کیمیکل کو ہٹانے یا دوبارہ تحلیل کرنے کے قابل ہونا چاہیے۔
اس معاملے میں ایک نئی لیبارٹری ٹیسٹ رگ کو HP/HTg پر انجیکشن پورٹس کے قریب بہنے والے حالات کو پروڈکشن سسٹم کے طور پر نقل کرنے کے لیے ڈیزائن کیا گیا تھا۔متحرک گن کنگ ٹیسٹ کے نتائج یہ ظاہر کرتے ہیں کہ مجوزہ ایپلی کیشن کی شرائط کے تحت سالوینٹ کا ایک اہم نقصان ریکارڈ کیا گیا تھا۔یہ تیزی سے گن کنگ اور بہاؤ لائنوں کو روکنے کا باعث بن سکتا ہے۔اس وجہ سے کام نے یہ ظاہر کیا کہ پانی کی پیداوار سے پہلے ان کنوؤں میں مسلسل کیمیائی انجیکشن کے لیے نسبتاً اہم خطرہ موجود تھا اور اس کے نتیجے میں اس فیلڈ کے لیے عام آغاز کے طریقہ کار کو ایڈجسٹ کرنے کا فیصلہ کیا گیا، جب تک پانی کی پیش رفت کا پتہ نہ چل گیا کیمیکل انجیکشن میں تاخیر ہوئی۔
مسلسل انجیکشن ڈاون ہول کے لیے اسکیل انحیبیٹر کی اہلیت میں انجیکشن پوائنٹ اور فلو لائن میں سالوینٹ سٹرپنگ اور گن کنگ آف دی اسکیل انحیبیٹر پر زیادہ فوکس تھا لیکن انجیکشن والو میں ہی گن کنگ کی صلاحیت کا اندازہ نہیں کیا گیا۔انجیکشن والو ممکنہ طور پر سالوینٹ کے اہم نقصان اور تیزی سے گن کنگ کی وجہ سے ناکام ہو گیا تھا۔,Fig.6.نتائج بتاتے ہیں کہ نظام کا ایک جامع نظریہ رکھنا ضروری ہے۔;نہ صرف پیداواری چیلنجوں پر توجہ دیں۔,لیکن کیمیکل کے انجیکشن سے متعلق چیلنجز بھی,یعنی انجیکشن والو۔
دوسرے شعبوں کا تجربہ
لمبی دوری کی کیمیکل انجیکشن لائنوں کے مسائل کے بارے میں ابتدائی رپورٹوں میں سے ایک گل فاک سینڈ ویگ ڈس سیٹلائٹ فیلڈز (اوسا ایٹل 2001) سے تھی .سب سی انجیکشن لائنوں کو پیدا ہونے والے سیالوں سے گیس کے حملے کی وجہ سے لائن کے اندر ہائیڈریٹ بننے سے روک دیا گیا تھا۔ انجیکشن والو کے ذریعے لائن میں۔ذیلی سمندری پیداوار کیمیکلز کی ترقی کے لیے نئی ہدایات تیار کی گئیں۔ضروریات میں ذرہ کو ہٹانا (فلٹریشن) اور پانی پر مبنی تمام پیمانے پر روکنے والوں میں ہائیڈریٹ انحیبیٹر (مثلاً گلائکول) کا اضافہ شامل ہے جو ذیلی سمندری ٹیمپلیٹس پر لگائے جائیں گے۔کیمیائی استحکام,viscosity اور مطابقت (مائع اور مواد) پر بھی غور کیا گیا۔ان ضروریات کو مزید Statoil سسٹم میں لے جایا گیا ہے اور اس میں ڈاون ہول کیمیکل انجیکشن بھی شامل ہے۔
Oseberg S یا فیلڈ کی ترقی کے مرحلے کے دوران یہ فیصلہ کیا گیا تھا کہ تمام کنوؤں کو DHC I سسٹمز (Fleming etal.2006) کے ساتھ مکمل کیا جائے۔ مقصد CaCO کو روکنا تھا۔۔ایس آئی انجیکشن کے ذریعہ اوپری نلیاں میں اسکیلنگ۔کیمیائی انجیکشن لائنوں کے حوالے سے ایک بڑا چیلنج سطح اور ڈاون ہول آؤٹ لیٹ کے درمیان مواصلت حاصل کرنا تھا۔کیمیکل انجیکشن لائن کا اندرونی قطر 7mm سے 0.7mm(ID) تک محدود ہو کر اینولس سیفٹی والو کے ارد گرد خلائی حدود اور اس حصے کے ذریعے مائع کی نقل و حمل کی صلاحیت نے کامیابی کی شرح کو متاثر کیا تھا۔پلیٹ فارم کے کئی کنوؤں میں کیمیکل انجیکشن لائنیں لگائی گئی تھیں۔,لیکن وجہ سمجھ نہیں آئی۔مختلف سیالوں کی ٹرینیں (glycol,خام,گاڑھا ہونا,xylene,پیمانے روکنے والا,پانی وغیرہ) کو viscosity اور مطابقت کے لیے لیبارٹری ٹیسٹ کیا گیا اور لائنوں کو کھولنے کے لیے آگے اور ریورس بہاؤ میں پمپ کیا گیا۔;البتہ,ٹارگٹ پیمانہ روکنے والے کو پورے طریقے سے کیمیکل انجیکشن والو تک پمپ نہیں کیا جا سکتا۔مزید,پیچیدگیاں ایک کنویں میں بقایا CaCl z مکمل کرنے والے نمکین پانی کے ساتھ فاسفونیٹ اسکیل انحیبیٹر کے ورن کے ساتھ اور گیسوئل کے اعلی تناسب اور کم پانی کی کٹوتی کے ساتھ کنویں کے اندر گن کنگ آف دی سکیل انحیبیٹر کے ساتھ دیکھی گئیں (Fleming etal.2006)
سبق سیکھا
ٹیسٹ کے طریقہ کار کی ترقی
DHC I سسٹمز کی ناکامی سے سیکھے گئے اہم اسباق پیمانے روکنے والے کی تکنیکی کارکردگی کے حوالے سے ہیں نہ کہ فعالیت اور کیمیائی انجیکشن کے حوالے سے۔ٹاپ سائیڈ انجیکشن اور سب سی انجیکشن نے اوور ٹائم اچھی طرح کام کیا ہے۔;البتہ,درخواست کو کیمیائی قابلیت کے طریقوں کی متعلقہ اپ ڈیٹ کے بغیر کیمیکل انجیکشن کو ڈاؤن ہول تک بڑھا دیا گیا ہے۔پیش کردہ دو فیلڈ کیسز سے Statoil کا تجربہ یہ ہے کہ اس قسم کی کیمیکل ایپلی کیشن کو شامل کرنے کے لیے گورننگ دستاویزات یا کیمیائی اہلیت کے لیے رہنما اصولوں کو اپ ڈیٹ کیا جانا چاہیے۔اہم دو چیلنجوں کی نشاندہی کی گئی ہے i) کیمیکل انجیکشن لائن میں خلا اور ii) کیمیکل کی ممکنہ بارش۔
کیمیکل کا بخارات پروڈکشن ٹیوبنگ پر ہو سکتا ہے (جیسا کہ گن کنگ کیس میں دیکھا گیا ہے) اور انجیکشن ٹیوبنگ میں (ویکیوم کیس میں ایک عارضی انٹرفیس کی نشاندہی کی گئی ہے) اس بات کا خطرہ ہے کہ یہ تیزاب بہاؤ کے ساتھ منتقل ہو سکتے ہیں اور انجیکشن والو میں اور مزید کنویں میں۔انجیکشن والو اکثر انجیکشن پوائنٹ کے فلٹر اپ اسٹریم کے ساتھ ڈیزائن کیا جاتا ہے۔,یہ ایک چیلنج ہے,جیسا کہ بارش کی صورت میں یہ فلٹر پلگ ہو سکتا ہے جس کی وجہ سے والو فیل ہو جاتا ہے۔
سیکھے گئے اسباق سے مشاہدات اور ابتدائی نتائج کے نتیجے میں مظاہر پر ایک وسیع لیبارٹری مطالعہ ہوا۔اس کا مجموعی مقصد مستقبل میں اسی طرح کے مسائل سے بچنے کے لیے قابلیت کے نئے طریقے تیار کرنا تھا۔اس مطالعے میں مختلف ٹیسٹ کیے گئے ہیں اور کئی لیبارٹری طریقوں کو ڈیزائن کیا گیا ہے (ترتیب میں تیار کیا گیا ہے) تاکہ شناخت شدہ چیلنجوں کے حوالے سے کیمیکلز کی جانچ کی جا سکے۔
● بند نظاموں میں رکاوٹیں اور مصنوعات کی استحکام کو فلٹر کریں۔
● کیمیکلز کی corrosivity پر جزوی سالوینٹس کے نقصان کا اثر۔
● ٹھوس یا چپچپا پلگوں کی تشکیل پر کیپلیری کے اندر جزوی سالوینٹ کے نقصان کا اثر۔
لیبارٹری کے طریقوں کے ٹیسٹ کے دوران کئی ممکنہ مسائل کی نشاندہی کی گئی ہے۔
● بار بار فلٹر کی رکاوٹیں اور خراب استحکام۔
● کیپلیری سے جزوی بخارات بننے کے بعد ٹھوس کی تشکیل
● سالوینٹ کے نقصان کی وجہ سے پی ایچ میں تبدیلی آتی ہے۔
کئے گئے ٹیسٹوں کی نوعیت نے کیپلیریوں کے اندر کیمیکلز کی طبعی خصوصیات میں تبدیلیوں سے متعلق اضافی معلومات اور علم بھی فراہم کیا ہے جب بعض شرائط کا نشانہ بنایا جاتا ہے۔,اور یہ اسی طرح کے حالات سے مشروط بلک حل سے کیسے مختلف ہے۔ٹیسٹ کے کام نے بلک سیال کے درمیان کافی فرق کی بھی نشاندہی کی ہے۔,بخارات کے مراحل اور بقایا سیال جو یا تو بارش اور/یا سنکنرن کی صلاحیت میں اضافہ کا باعث بن سکتے ہیں۔
پیمانہ روکنے والوں کی corrosivity کے لیے ٹیسٹ کا طریقہ کار تیار کیا گیا تھا اور اسے گورننگ دستاویزات میں شامل کیا گیا تھا۔ہر ایک ایپلی کیشن کے لیے توسیعی corrosivity ٹیسٹنگ کی جانی تھی اس سے پہلے کہ اسکیل inhibitor کے انجیکشن کو لاگو کیا جا سکے۔انجیکشن لائن میں موجود کیمیکل کے گن کنگ ٹیسٹ بھی کیے گئے ہیں۔
کیمیکل کی قابلیت شروع کرنے سے پہلے کام کا ایک دائرہ کار بنانا ضروری ہے جو چیلنجوں اور کیمیکل کے مقصد کو بیان کرے۔ابتدائی مرحلے میں اہم چیلنجوں کی نشاندہی کرنا ضروری ہے تاکہ وہ کیمیکل کی اقسام کو منتخب کر سکیں جو مسئلہ کو حل کریں گے۔قبولیت کے اہم ترین معیارات کا خلاصہ جدول 2 میں پایا جا سکتا ہے۔
کیمیکلز کی اہلیت
کیمیکلز کی اہلیت ہر درخواست کے لیے جانچ اور نظریاتی تشخیص دونوں پر مشتمل ہوتی ہے۔تکنیکی تفصیلات اور ٹیسٹ کے معیار کی وضاحت اور قائم کی جانی چاہئے۔,مثال کے طور پر HSE کے اندر,مواد کی مطابقت,مصنوعات کی استحکام اور مصنوعات کے معیار (ذرات).مزید,نقطہ انجماد,viscosity اور دوسرے کیمیکلز کے ساتھ مطابقت,ہائیڈریٹ روکنے والا,تشکیل شدہ پانی اور پیدا ہونے والے سیال کا تعین کرنا ضروری ہے۔ٹیسٹ کے طریقوں کی ایک آسان فہرست جو کیمیکلز کی اہلیت کے لیے استعمال کی جا سکتی ہے جدول 2 میں دی گئی ہے۔
تکنیکی کارکردگی پر مسلسل توجہ اور نگرانی,خوراک کی شرح اور HSE حقائق اہم ہیں۔کسی پروڈکٹ کی ضروریات کسی فیلڈ یا پروسیس پلانٹ کی زندگی بھر میں بدل سکتی ہیں۔۔پیداوار کی شرح کے ساتھ ساتھ سیال کی ساخت کے ساتھ مختلف ہوتی ہے۔کارکردگی کی تشخیص کے ساتھ فالو اپ سرگرمی,بہترین علاج کے پروگرام کو یقینی بنانے کے لیے نئے کیمیکلز کی اصلاح اور/یا جانچ کثرت سے کی جانی چاہیے۔
تیل کے معیار پر منحصر ہے۔,آف شور پروڈکشن پلانٹ میں پانی کی پیداوار اور تکنیکی چیلنجز,برآمدی معیار کو حاصل کرنے کے لیے پروڈکشن کیمیکلز کا استعمال ضروری ہو سکتا ہے۔,ریگولیٹری کی ضروریات,اور آف شور تنصیب کو محفوظ طریقے سے چلانے کے لیے۔تمام شعبوں میں مختلف چیلنجز ہیں، اور پیداواری کیمیکلز کی ضرورت فیلڈ سے فیلڈ اور اوور ٹائم میں مختلف ہوگی۔
قابلیت کے پروگرام میں پیداواری کیمیکلز کی تکنیکی کارکردگی پر توجہ مرکوز کرنا ضروری ہے۔,لیکن کیمیکل کی خصوصیات پر توجہ مرکوز کرنا بھی بہت ضروری ہے۔,جیسے استحکام,مصنوعات کے معیار اور مطابقت.اس ترتیب میں مطابقت کا مطلب سیالوں کے ساتھ مطابقت ہے۔,مواد اور دیگر پیداواری کیمیکل۔یہ ایک چیلنج ہو سکتا ہے۔کسی مسئلے کو حل کرنے کے لیے کیمیکل کا استعمال کرنا مناسب نہیں ہے تاکہ بعد میں پتہ چل سکے کہ کیمیکل نئے چیلنجوں میں حصہ ڈالتا ہے یا پیدا کرتا ہے۔یہ شاید کیمیکل کی خصوصیات ہیں نہ کہ تکنیکی چیلنج جو کہ سب سے بڑا چیلنج ہے۔
خصوصی ضروریات
سپلائی شدہ مصنوعات کی فلٹریشن پر خصوصی تقاضوں کا اطلاق ذیلی نظام اور مسلسل انجیکشن ڈاون ہول کے لیے کیا جانا چاہیے۔کیمیکل انجیکشن سسٹم میں سٹرینرز اور فلٹرز ٹاپ سائیڈ انجیکشن سسٹم سے ڈاون اسٹریم آلات کی تفصیلات کی بنیاد پر فراہم کیے جائیں۔,پمپ اور انجکشن والوز,ڈاون ہول انجیکشن والوز تک۔جہاں کیمیکلز کا ڈاون ہول لگاتار انجیکشن لگایا جاتا ہے کیمیکل انجیکشن سسٹم میں تصریح سب سے زیادہ تنقید کے ساتھ تصریح پر مبنی ہونی چاہیے۔یہ انجیکشن والو کے نیچے کا فلٹر ہوسکتا ہے۔
انجیکشن چیلنجز
انجیکشن سسٹم کا مطلب نال کے ذیلی سمندری بہاؤ کا 3-50 کلومیٹر کا فاصلہ اور کنویں میں 1-3 کلومیٹر نیچے ہے۔جسمانی خصوصیات جیسے viscosity اور کیمیکلز کو پمپ کرنے کی صلاحیت اہم ہیں۔اگر سمندری تہہ کے درجہ حرارت پر واسکاسیٹی بہت زیادہ ہے تو یہ کیمیکل کو کیمیکل انجیکشن لائن کے ذریعے زیر آب نال اور زیر سمندر انجیکشن پوائنٹ یا کنویں میں پمپ کرنا ایک چیلنج ہوسکتا ہے۔viscosity متوقع اسٹوریج یا آپریشنل درجہ حرارت پر نظام کی تفصیلات کے مطابق ہونا چاہئے.اس کا ہر معاملے میں جائزہ لینا چاہیے۔,اور نظام پر منحصر ہوگا۔جیسا کہ ٹیبل کیمیکل انجیکشن کی شرح کیمیائی انجیکشن میں کامیابی کا ایک عنصر ہے۔کیمیائی انجیکشن لائن کو پلگ کرنے کے خطرے کو کم کرنے کے لیے,اس نظام میں موجود کیمیکلز کو ہائیڈریٹ سے روکا جانا چاہئے (اگر ہائیڈریٹس کا امکان ہو)۔سسٹم میں موجود سیالوں کے ساتھ مطابقت (تحفظ سیال) اور ہائیڈریٹ روکنے والے کو انجام دینا ہوگا۔اصل درجہ حرارت پر کیمیکل کے استحکام کے ٹیسٹ (کم سے کم ممکنہ محیطی درجہ حرارت,وسیع درجہ حرارت,زیر سمندر درجہ حرارت,انجیکشن درجہ حرارت) کو گزرنا ہوگا۔
دی گئی فریکوئنسی پر کیمیائی انجیکشن لائنوں کو دھونے کے پروگرام پر بھی غور کیا جانا چاہیے۔کیمیکل انجیکشن لائن کو سالوینٹس کے ساتھ باقاعدگی سے فلش کرنے سے یہ ایک حفاظتی اثر دے سکتا ہے۔,گلائکول یا کلیننگ کیمیکل جمع ہونے سے پہلے ممکنہ ذخائر کو دور کرنے کے لیے اور لائن کو پلگ کرنے کا سبب بن سکتا ہے۔فلشنگ سیال کا منتخب کیمیائی محلول ہونا چاہیے۔انجیکشن لائن میں کیمیکل کے ساتھ ہم آہنگ۔
بعض صورتوں میں کیمیکل انجیکشن لائن کا استعمال فیلڈ لائف ٹائم اور سیال حالات کے دوران مختلف چیلنجوں کی بنیاد پر کئی کیمیائی ایپلی کیشنز کے لیے کیا جاتا ہے۔پانی کی پیش رفت سے پہلے ابتدائی پیداواری مرحلے میں اہم چیلنجز ان سے مختلف ہو سکتے ہیں جو زندگی کے آخر میں اکثر پانی کی پیداوار میں اضافے سے متعلق ہوتے ہیں۔غیر آبی سالوینٹ کی بنیاد پر روکنے والے جیسے اسفالٹ اینی انحیبیٹر سے پانی پر مبنی کیمیکل جیسے اسکیل انحیبیٹر میں تبدیل کرنا مطابقت کے ساتھ چیلنج دے سکتا ہے۔لہذا جب کیمیکل انجیکشن لائن میں کیمیکل تبدیل کرنے کا منصوبہ بنایا جاتا ہے تو مطابقت اور قابلیت اور سپیسرز کے استعمال پر توجہ مرکوز کرنا ضروری ہے۔
مواد
مواد کی مطابقت کے بارے میں,تمام کیمیکل سیل کے ساتھ ہم آہنگ ہونا چاہئے,elastomers,کیمیکل انجیکشن سسٹم اور پروڈکشن پلانٹ میں استعمال ہونے والی گسکیٹ اور تعمیراتی مواد۔مسلسل انجیکشن ڈاون ہول کے لیے کیمیکلز (مثلاً تیزابی پیمانہ روکنے والا) کی corrosivity کے لیے ٹیسٹ کا طریقہ کار تیار کیا جانا چاہیے۔ہر درخواست کے لیے کیمیکلز کے انجیکشن کو لاگو کرنے سے پہلے توسیع شدہ corrosivity ٹیسٹنگ کی جانی چاہیے۔
بحث
مسلسل ڈاون ہول کیمیکل انجیکشن کے فوائد اور نقصانات کا جائزہ لینا ہوگا۔ڈی ایچ ایس کی حفاظت کے لیے اسکیل انحیبیٹر کا لگاتار انجیکشن لگانا کنویں کو پیمانے سے بچانے کے لیے پروڈکشن ٹیوبنگ ایک خوبصورت طریقہ ہے۔جیسا کہ اس مقالے میں بتایا گیا ہے کہ مسلسل ڈاون ہول کیمیکل انجیکشن کے ساتھ کئی چیلنجز ہیں۔,تاہم خطرے کو کم کرنے کے لیے حل سے منسلک مظاہر کو سمجھنا ضروری ہے۔
خطرے کو کم کرنے کا ایک طریقہ ٹیسٹ کے طریقہ کار کی ترقی پر توجہ مرکوز کرنا ہے۔اوپر کی طرف یا زیر سمندر کیمیکل انجیکشن کے مقابلے میں کنویں کے نیچے مختلف اور زیادہ شدید حالات ہیں۔کیمیکل ڈاون ہول کے مسلسل انجیکشن کے لیے کیمیکل کے لیے قابلیت کے طریقہ کار کو حالات میں ان تبدیلیوں کو مدنظر رکھنا ہوتا ہے۔کیمیکلز کی اہلیت اس مواد کے مطابق کی جانی چاہیے جس سے کیمیکل رابطے میں آسکتے ہیں۔مطابقت کی اہلیت اور ان حالات میں جانچ کے تقاضے جو ممکن حد تک قریب سے نقل کرتے ہیں ان مختلف طرز زندگی کے حالات جن کے تحت یہ نظام کام کریں گے کو اپ ڈیٹ اور لاگو کرنا ہوگا۔ٹیسٹ کے طریقہ کار کو مزید حقیقت پسندانہ اور نمائندہ ٹیسٹوں کے لیے تیار کیا جانا چاہیے۔
اس کے علاوہ,کیمیکلز اور آلات کے درمیان تعامل کامیابی کے لیے ضروری ہے۔انجیکشن کیمیکل والوز کی نشوونما میں کیمیائی خصوصیات اور کنویں میں انجیکشن والو کے مقام کو مدنظر رکھنا ہوتا ہے۔جانچ کے آلات کے حصے کے طور پر اصلی انجیکشن والوز کو شامل کرنے اور اہلیت کے پروگرام کے حصے کے طور پر اسکیل انحیبیٹر اور والو ڈیزائن کی کارکردگی کی جانچ کو انجام دینے پر غور کیا جانا چاہئے۔پیمانہ روکنے والوں کو کوالیفائی کرنے کے لیے,بنیادی توجہ اس سے قبل عمل کے چیلنجوں اور پیمانے پر روکنا پر رہی ہے۔,لیکن اچھے پیمانے پر روکنا مستحکم اور مسلسل انجیکشن پر منحصر ہے۔مستحکم اور مسلسل انجیکشن کے بغیر پیمانے کے امکانات بڑھ جائیں گے۔اگر اسکیل انہیبیٹر انجیکشن والو گنک ایڈ ہے اور فلوڈ اسٹریم میں اسکیل انحیبیٹر انجیکشن نہیں ہے,کنویں اور حفاظتی والوز پیمانے سے محفوظ نہیں ہیں اور اس وجہ سے محفوظ پیداوار خطرے میں پڑ سکتی ہے۔اہلیت کے طریقہ کار کو عمل کے چیلنجوں اور اہل پیمانے پر روکنے والے کی کارکردگی کے علاوہ پیمانے پر روکنے والے کے انجیکشن سے متعلق چیلنجوں کا خیال رکھنا ہوتا ہے۔
نئے نقطہ نظر میں متعدد مضامین شامل ہیں اور نظم و ضبط اور متعلقہ ذمہ داریوں کے درمیان تعاون کو واضح کرنا ہوگا۔اس ایپلی کیشن میں ٹاپ سائیڈ پروسیس سسٹم,subsea ٹیمپلیٹس اور اچھی طرح سے ڈیزائن اور تکمیل شامل ہیں۔کیمیکل انجیکشن سسٹم کے لیے مضبوط حل تیار کرنے پر توجہ مرکوز کرنے والے ملٹی ڈسپلن نیٹ ورکس اہم ہیں اور شاید کامیابی کا راستہ۔مختلف شعبوں کے درمیان بات چیت اہم ہے۔;خاص طور پر کیمسٹوں کے درمیان قریبی رابطہ ضروری ہے جن کے پاس لگائے گئے کیمیکلز کا کنٹرول ہے اور کنویں کے انجینئرز جن کے پاس کنویں میں استعمال ہونے والے آلات کا کنٹرول ہے۔مختلف شعبوں کے چیلنجوں کو سمجھنا اور ایک دوسرے سے سیکھنا پورے عمل کی پیچیدگی کو سمجھنے کے لیے ضروری ہے۔
نتیجہ
● ڈی ایچ ایس کی حفاظت کے لیے اسکیل انحیبیٹر کا لگاتار انجیکشن یا پروڈکشن نلیاں کنویں کی حفاظت کے لیے ایک خوبصورت طریقہ ہے۔
● شناخت شدہ چیلنجوں کو حل کرنا,مندرجہ ذیل سفارشات ہیں:
● ایک وقف شدہ DHCI اہلیت کا طریقہ کار انجام دینا ضروری ہے۔
● کیمیائی انجیکشن والوز کے لیے قابلیت کا طریقہ
● کیمیائی فعالیت کے لیے ٹیسٹ اور قابلیت کے طریقے
● طریقہ کار کی ترقی
● متعلقہ مواد کی جانچ
● کثیر الضابطہ تعامل جہاں شامل مختلف شعبوں کے درمیان مواصلت کامیابی کے لیے اہم ہے۔
اعترافات
مصنف اس کام کو شائع کرنے کی اجازت کے لیے Statoil AS A کا شکریہ ادا کرنا چاہتا ہے اور تصویر 2 میں تصویر کے استعمال کی اجازت دینے کے لیے Baker Hughes اور Schlumberger کا شکریہ ادا کرنا چاہتا ہے۔
نام بندی
(Ba/Sr)SO4=بیریم/سٹرونٹیم سلفیٹ
CaCO3 = کیلشیم کاربونیٹ
DHCI=ڈاؤن ہول کیمیکل انجیکشن
DHSV=ڈاؤن ہول سیفٹی والو
مثال کے طور پر = مثال کے طور پر
GOR = گیس کا تناسب
HSE=صحت کی حفاظت کا ماحول
HPHT=ہائی پریشر ہائی درجہ حرارت
ID=اندرونی قطر
یعنی = یعنی
کلومیٹر = کلومیٹر
ملی میٹر = ملی میٹر
ایم ای جی = مونو ایتھیلین گلائکول
mMD=میٹر ناپی گئی گہرائی
OD = بیرونی قطر
SI=پیمانہ روکنے والا
mTV D=میٹر کل عمودی گہرائی
U-tube=U شکل والی ٹیوب
VPD = بخارات کے دباؤ کو دبانے والا
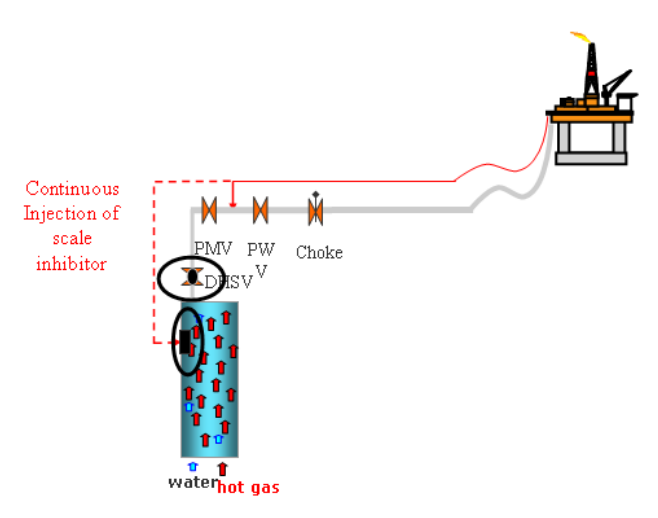
شکل 1. atypical فیلڈ میں subsea اور downhole کیمیکل انجیکشن سسٹم کا جائزہ۔کیمیکل انجیکشن اپ اسٹریم DHSV اور متعلقہ متوقع چیلنجوں کا خاکہ۔DHS V=ڈاون ہول سیفٹی والو، PWV=پروسیس ونگ والو اور PM V=پروسیس ماسٹر والو۔
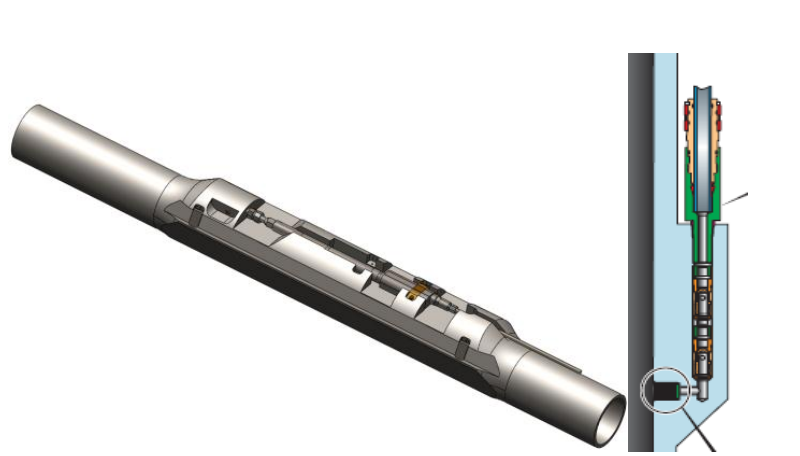
شکل 2۔ مینڈریل اور والو کے ساتھ غیر معمولی ڈاون ہول کیمیکل انجیکشن سسٹم کا خاکہ۔یہ نظام کئی گنا سطح تک جڑا ہوا ہے، اس کے ذریعے کھلایا جاتا ہے اور نلکی کے کنڈلی طرف والے نلکے کے ہینگر سے منسلک ہوتا ہے۔کیمیائی انجیکشن مینڈریل کو روایتی طور پر کیمیکل تحفظ دینے کے ارادے سے کنویں میں گہرائی میں رکھا جاتا ہے۔
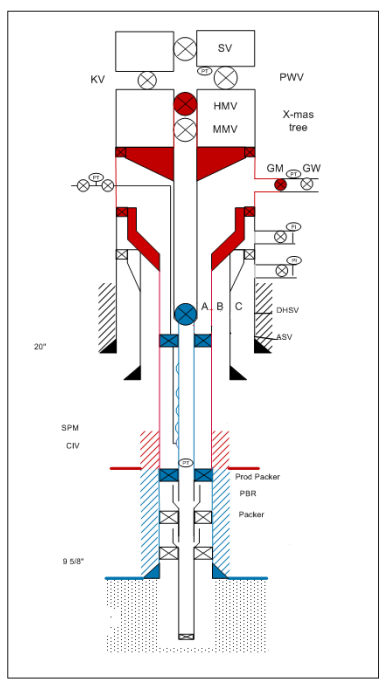
شکل 3. عام کنواں رکاوٹ منصوبہ بندی,جہاں نیلا رنگ بنیادی کنویں رکاوٹ والے لفافے کی نمائندگی کرتا ہے۔اس صورت میں پیداوار نلیاں.سرخ رنگ ثانوی رکاوٹ کے لفافے کی نمائندگی کرتا ہے۔سانچےبائیں طرف کیمیکل انجیکشن کی طرف اشارہ کیا گیا ہے، انجکشن کے ساتھ بلیک لائن اس علاقے میں پروڈکشن نلیاں کی طرف اشارہ کیا گیا ہے جس پر سرخ نشان (ثانوی رکاوٹ) ہے۔
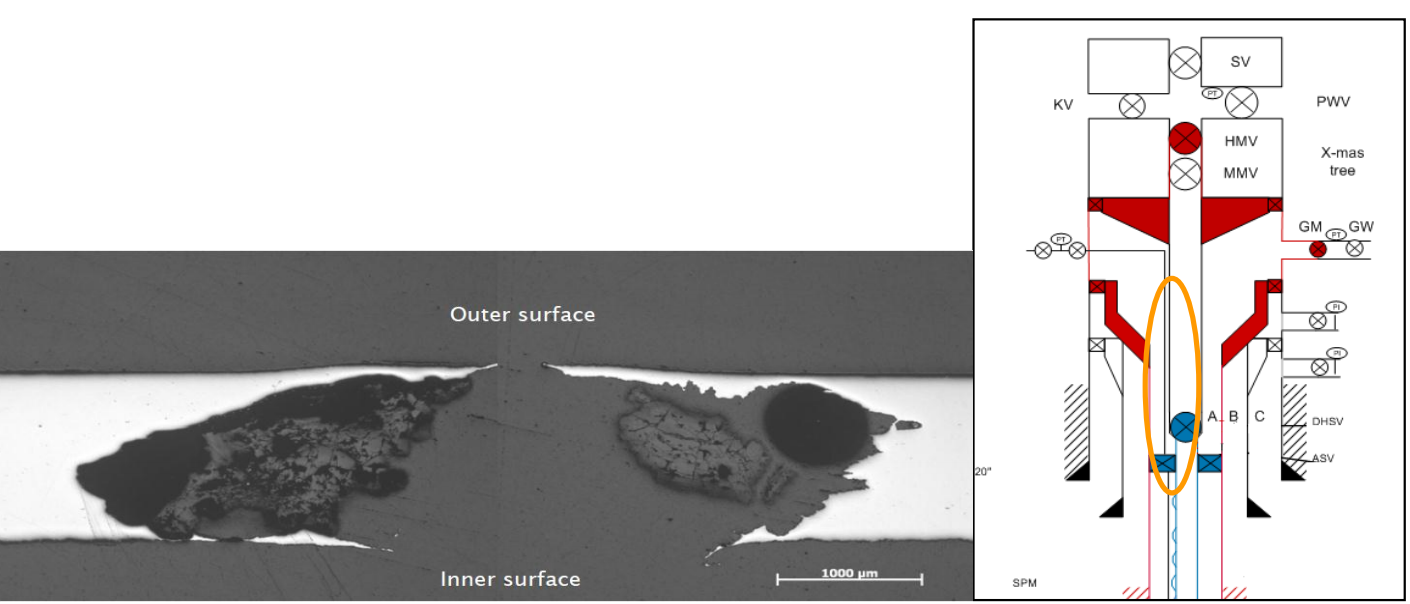
شکل 4. 3/8" انجیکشن لائن کے اوپری حصے میں پایا جانے والا سوراخ۔یہ علاقہ atypical well barrier schematic کے خاکے میں دکھایا گیا ہے، جو نارنجی بیضوی سے نشان زد ہے۔
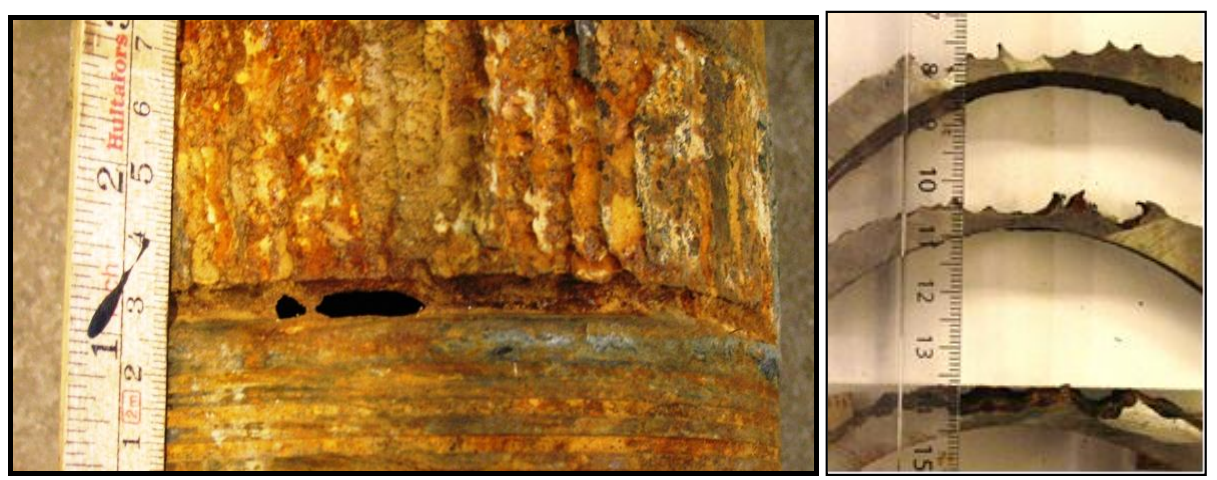
شکل 5۔ 7” 3% کروم نلیاں پر شدید سنکنرن کا حملہ۔یہ اعداد و شمار سنکنرن کے حملے کو ظاہر کرتا ہے جب اسکیل انحیبیٹر کو پٹڈ کیمیکل انجیکشن لائن سے پروڈکشن نلیاں تک اسپرے کیا جاتا ہے۔
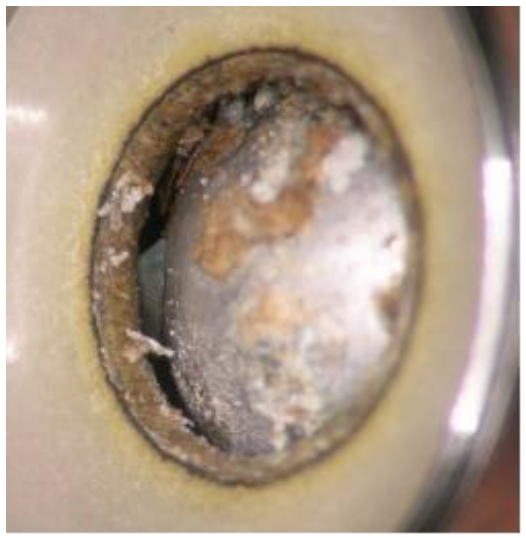
تصویر 6. کیمیکل انجیکشن والو میں ملا ملبہ۔اس معاملے میں ملبہ کچھ سفید ملبے کے علاوہ شاید تنصیب کے عمل سے دھات کی شیونگ تھی۔سفید ملبے کی جانچ سے یہ ثابت ہوا کہ کیمیکل انجیکشن کی طرح کیمسٹری والے پولیمر تھے۔
پوسٹ ٹائم: اپریل 27-2022